PROJECTS
PDF BigDog Quadruped Robot Control Board
System Overview
Boston Dynamics implemented BigDog with a variety of COTS (Commercial Off The Shelf) computing hardware. Bolton Engineering worked with Boston Dynamics to develop a flexible high-speed general purpose "robotics toolkit" PC-104+ PCI bus interface board using an Intel/Altera FPGA. The board contained on-board power supplies to convert battery power to several required system voltages as well as a variety of general purpose hardware:
- Eight Motor Quadrature Encoder interfaces (in FPGA)
- Thirty-three channel expandable A/D converter and sixteen channel D/A converter
- Serial interface to sensors (in FPGA)
- Four serial ports, configurable as either RS-232 or RS-485 (in FPGA)
- Forty-eight lines digital I/O, with level converters
- Eight-channel RC-servo interface (in FPGA)
- Expandable connector slot into which boards with new functionality may be placed
- Multi-Voltage Power Supply, for on-board logic and for other system electronics
Project Scope
Bolton Engineering wrote the specification, designed the schematics and circuit board, developed and simulated the Intel/Altera FPGA (Field Programmable Gate Array) I/O system, fabricated and debugged the hardware. Boston Dynamics was responsible for all system, navigation, communications and control software. The project was completed in twelve weeks, on schedule for a company demonstration. The first-pass boards performed all required functions and required only minor design changes.
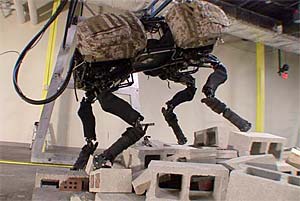
BigDog is the biggest and boldest of Boston Dynamics' robots. BigDog is a rough-terrain walking robot that can run, climb and carry heavy loads. BigDog has four articulated legs with compliant elements that absorb shock and recycle energy from one step to the next. BigDog weighs 240 pounds, and is the size of a large dog or small mule: about 3 feet long, 2.5 feet high.
BigDog's on-board computer controls locomotion, servos the legs and monitors a variety of sensors. BigDog's control system maintains balance, navigates, and adjusts system kinetics as conditions change. Sensors for locomotion include joint position, joint force, ground contact, ground load, a gyroscope, LIDAR and a stereo vision system. Other sensors monitor the internal state of BigDog: hydraulic pressure, oil temperature, engine functions, and battery charge.
Click here to view BigDog videos on YouTube.